Much like outdated machinery, old moulds often linger in storage long after serving their purpose. Decommissioning them efficiently is becoming increasingly important, as they take up valuable space and incur unnecessary costs. A standardised decommissioning process aims to address this issue, ensuring that every step is handled with care and precision. However, executing an effective decommissioning strategy can be complex due to the planning and coordination required. Despite these challenges, responsible mould decommissioning is essential for both the moulder and their business partners.
In our previous article titled “Part 4 – Is your Mould on the Right “Track”?”, we discussed how to track mould condition and implement strategies to it. This article covers the decommissioning of moulds and concludes our 5-part series on Mould Lifecycle Management (MLM).
Why Decommission moulds?
A mould, like another piece of machinery, has an end-of-life to it. It could be rendered obsolete due to several reasons:
- The mould life has elapsed: The mould has been used extensively, having undergone several maintenance and refurbishment activities. The elements of the mould have worn out to the extent that they must be replaced. Replacing all the worn-out elements would more or less amount to replacing all the mould elements.
- Product relaunch or design change: A new product format has replaced the existing format produced from this mould; hence, the moulder has no volume demands from this mould.
- Mould is no longer in use: The mould has been kept in storage for a very long duration.
In all three cases, the obsolete mould occupies space and incurs storage costs. Converters often find themselves lacking space to store moulds not in use. Hence, it is prudent to decommission these moulds safely and responsibly at the earliest.
Methods of Mould Decommissioning
Depending on the category and condition of the equipment, you can choose from different decommissioning methods:
- Recycling/cannibalising: Scavenge useful mould elements to use in a different mould. You can also scavenge useful elements of the cavity stack and use them in a copy mould with the same design. (A like-for-like replacement insert of a worn-out mould will not be always possible. Toolroom managers should assess the condition and usability of the insert before installing it in the copy mould).
- Scrap: Perhaps the easiest way to decommission the mould, scraping the mould entails selling it to a scrapyard agent, enabling the converter or OEM to recoup a small amount of money for the discarded metal. Depending on the volume of the mould steel to be scrapped, the recouped amount can be significant enough to perform maintenance of other active moulds.
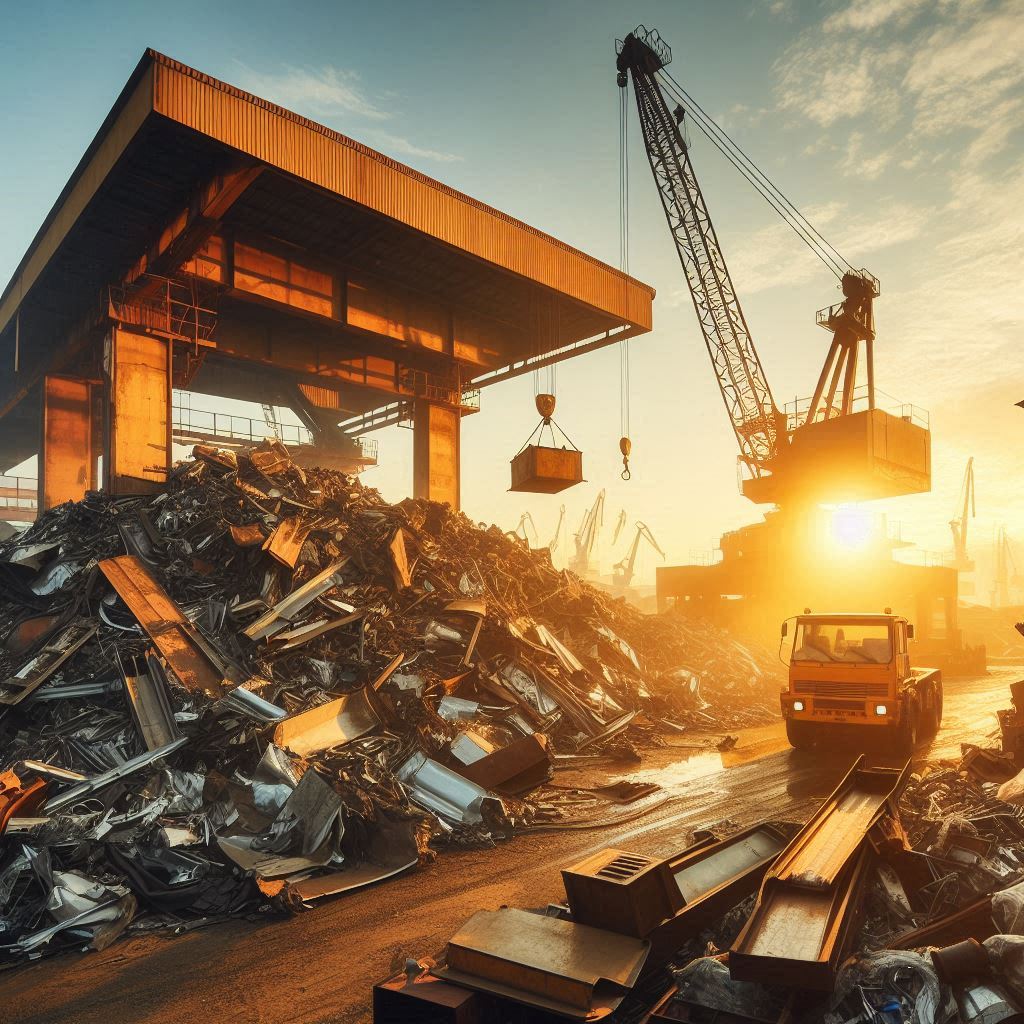
- Physical destruction of the core and cavity inserts: If you have manufactured a mould to produce a proprietary plastic product for a client, the client often insists that the cores and cavities are damaged to an extent where they cannot be recovered at the end-of-life of the mould, thus maintaining the exclusivity of the client’s product design. This mode of decommissioning requires you to generate a certificate of mould destruction and share it with your client. A third-party entity may also be involved to verify that the destruction has been done satisfactorily so that the mould cannot be used in whole or in part for its original purpose i.e., the production of plastic products.
Process
The process for decommissioning the moulds should be as follows:
- Confirm the remaining life span of the mould: Check your quarterly/bi-annual mould tracking report to determine the current condition of the mould. You may refer to past tracking data from the time when the mould was last in production.
- Connect with stakeholders: Determine if the mould is ‘usable’ or ‘not usable’. If the mould is usable or if there are plans to use the mould again in the future, pack and store the mould at your storage facility or warehouse. If the mould is not usable, connect with stakeholders and inform them about your plan to decommission the mould.
- Plan the Full Completion of the decommissioning: Create a network of the milestones – physical destruction of the core and cavities, collecting pictures, verification by a 3rd party auditor, generating a certificate of mould destruction, etc.
- Physical Destruction: The physical destruction of the cavities can be done by:
- Welding torch
- Angle grinder
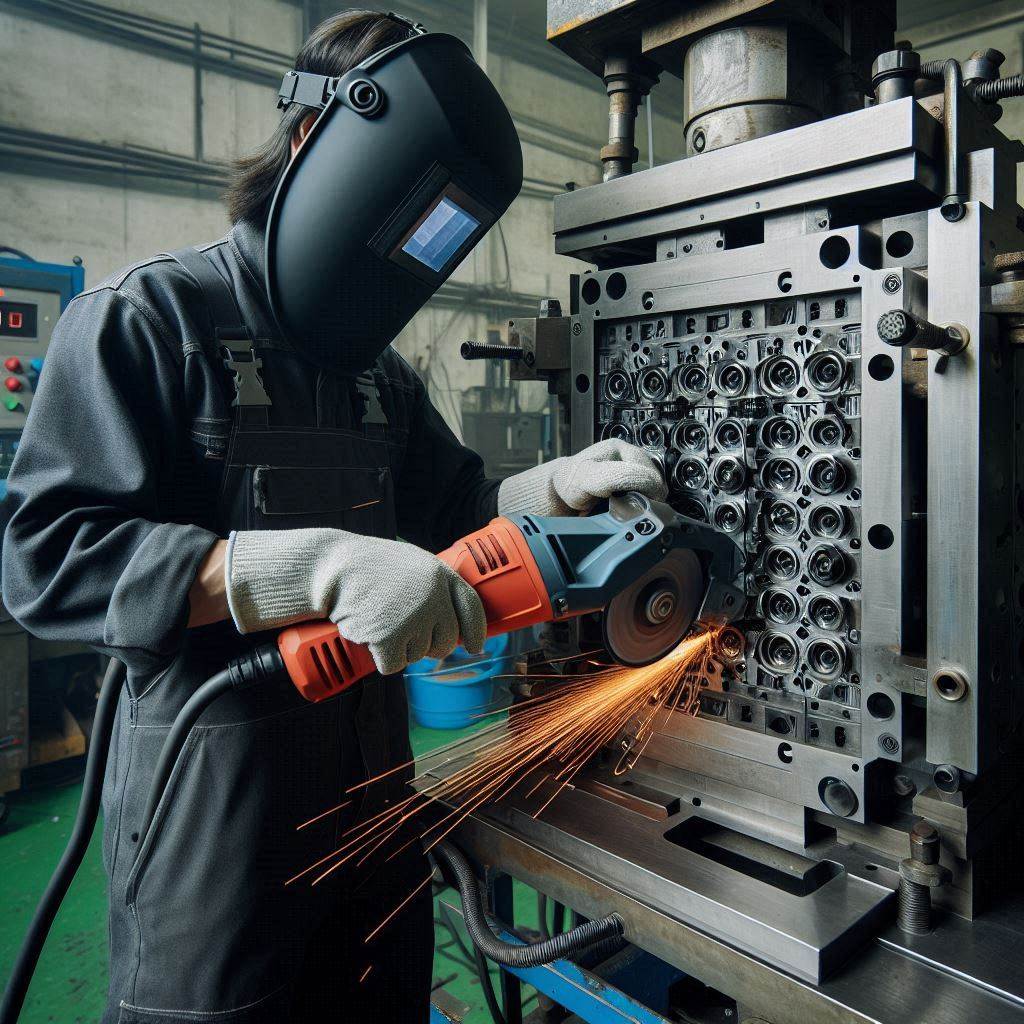
- Photograph the mould before the destruction: Include the mould serial number, and then photograph each destroyed mould after the destruction to include the mould serial number.
- Generate a certificate of mould destruction: Use your company letterhead or the company destroying the mould.
- Share the certificate of mould destruction: Provide the certificate to your client for record-keeping.
With this, we have come to the end of our 5-part series on Mould Lifecycle Management (MLM). Throughout these five articles, we have delved into the planning and commissioning of the mould, preventive and corrective maintenance strategies, tracking mould performance, and the eventual decommissioning of the mould.
You can find the link to the articles here
Mould Lifecycle Management: Part 1 – https://www.efficientinnovations.in/mould-lifecycle-management
Mould Lifecycle Management (MLM): Part 2 – https://www.efficientinnovations.in/mould-lifecycle-management-mlm-commissioning
Mould Lifecycle Management (MLM): Part 3.1 – https://www.efficientinnovations.in/part-3-1-mould-lifecycle-management-mlm-preventive-maintenance
Mould Lifecycle Management: Corrective Maintenance – https://www.efficientinnovations.in/mould-lifecycle-management-corrective-maintenance
Part 4 – Is you Mould on the Right “Track”? – https://www.efficientinnovations.in/part-4-is-your-mould-on-the-right-track
Efficient Innovations has been supporting its varied clients for over a decade, providing a single-stop solution for all their mould lifecycle management needs. Reach out to us at www.efficientinnovations.in to know more.
BY ERWIN JOSEPH
www.linkedin.com/in/erwin-joseph-vadukut
About the author: The author is a Project Manager at Efficient Innovations and has experience of managing multiple Mould Lifecycle Management (MLM) projects for varied clients in the FMCG industry.