The Second Step
Let us take our journey to the next step.
In our previous article of Mould Lifecycle Management (MLM), we discussed the planning stage. Stakeholders / Key Decision Makers (KDM’s) have given their green signal to move our train to the next station, a station called Commissioning.
In case you missed the previous article, below you can find a link for same.
Journey is, of course, more important than the destination!
Similarly, the pathway to successful production mould comes to life only during the production run.
Commissioning Stage
The output of this stage is a production mould supporting your brand/company by syncing it with the market demands. Process which delivers a successful production mould is as follows:
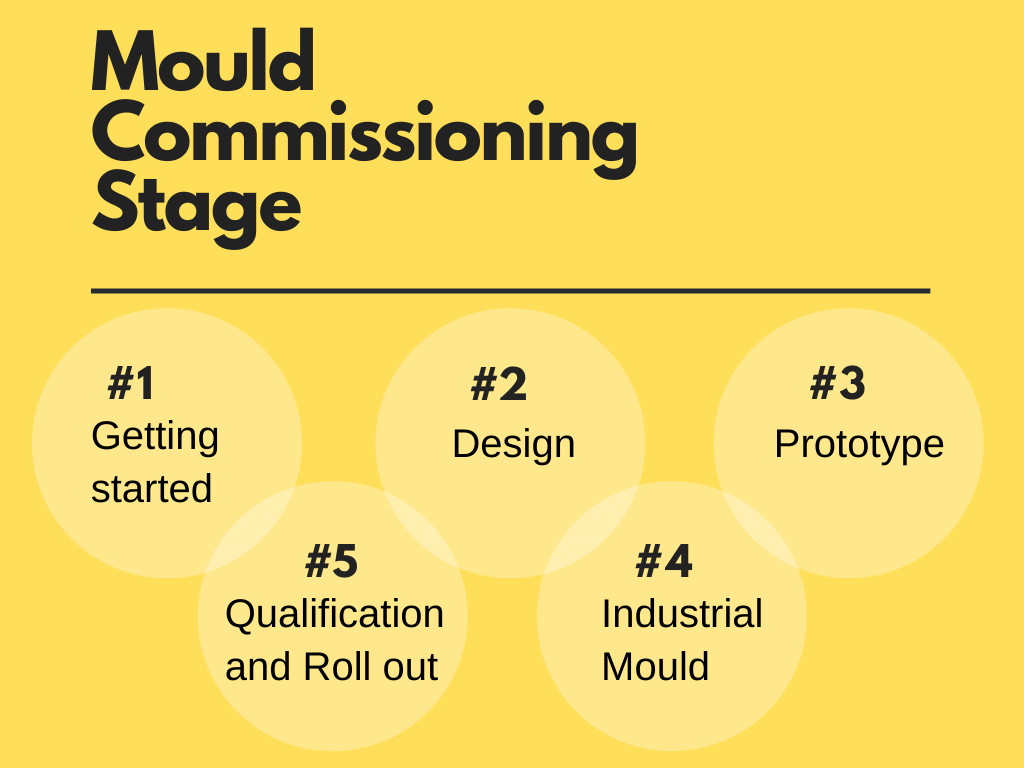
1. Getting Started: Every mammoth structure starts with a humble brick. Commissioning too starts with a tiny step – a PO to your supplier which is a financial confirmation to move ahead with the mould building process.
Depending on whether the mould is for innovation or a repeat one, various parameters viz. previous learnings, CT optimization, new technology, maintenance-friendly design etc. are considered.
2. Design: Mould manager must ensure completion of technical preparation works and bring all team members on the same page w.r.t. the overall mould design.
Preparation works include:
- Sharing part details with the mould maker
- PO for the required work
- Initial design review meetings for call outs, if any
- Mould-machine compatibility
- Any other project-specific work
Attendees for this discussion must include the:
- Mould maker
- Mould manager
- R&D team
- SME
- Supplier
- Owner of the mould / brand as an optional attendee
3. Prototype: After the above discussion, manufacture the prototype if it is a new product launch.
The prototype:
- Can be a single or multiple cavity mould.
- Is examined via trials to check functionality of the mould along with the functional, dimensional and aesthetic aspect of the plastic part.
Skip this step for an existing mould provided the mould maker is confident enough.
4. Production / Industrial Mould: Discuss the learnings, if any, from the Prototype stage and ask the mould maker to present the final mould design to the team.
On approval of the final mould design, the mould maker confirms if the lead time to build a new mould remains the same as quoted or otherwise. Any fresh learnings from the prototype mould may affect the overall Lead time.
It is in this stage that our product begins to take tangible form.
5. Qualification & Roll-out: Mould trial is the most important checkpoint and is the final gate to confirm the mould’s readiness for production.
Tons of planning is involved in a successful mould trial and all preparations must be completed earlier. The recommended location for the first mould trial is the workshop where it is manufactured. Conduct the retrial at the site where it will be running for production i.e. in the production environment.
Mould trials are performed in phases:
- First phase is a short trial to understand the mould functioning and part aesthetics.
- Final trials are conducted once the mould maker is confident on the mould steel dimensions. These check the mould functionality along with the functional, dimensional, and aesthetic aspect of the plastic part.
As mould managers, we at Efficient Innovations Pvt. Ltd. ensure that Scientific Injection Moulding tests are performed and Balance Of Fill is checked in order to optimize the process window to run the mould.
Trialing the samples at filling lines ensures that there are no issues in the entire filling line and also during assembly of the product.
Document the entire trial plan and the outcomes for future use. The document must include key parameters such as:
- The CT at which the mould ran
- Issues observed, if any
- Further actions
- Important mould dimensions
- Significant part dimensions
- Material details
- Process parameters
- Other important data specific to the mould
On completion of the mould trials and approval of samples by relevant Stakeholders, the mould is ready to be shipped out to the site where it will run for production orders.
After shipping the mould to the Supplier or the site, the mould is trialled and the samples are again shipped to the relevant stakeholders for approval. Thereafter, the mould starts its production run.
Commissioning Guidelines for Mould Managers
If you are a mould manager, following factors will prove invaluable during the course of mould build:
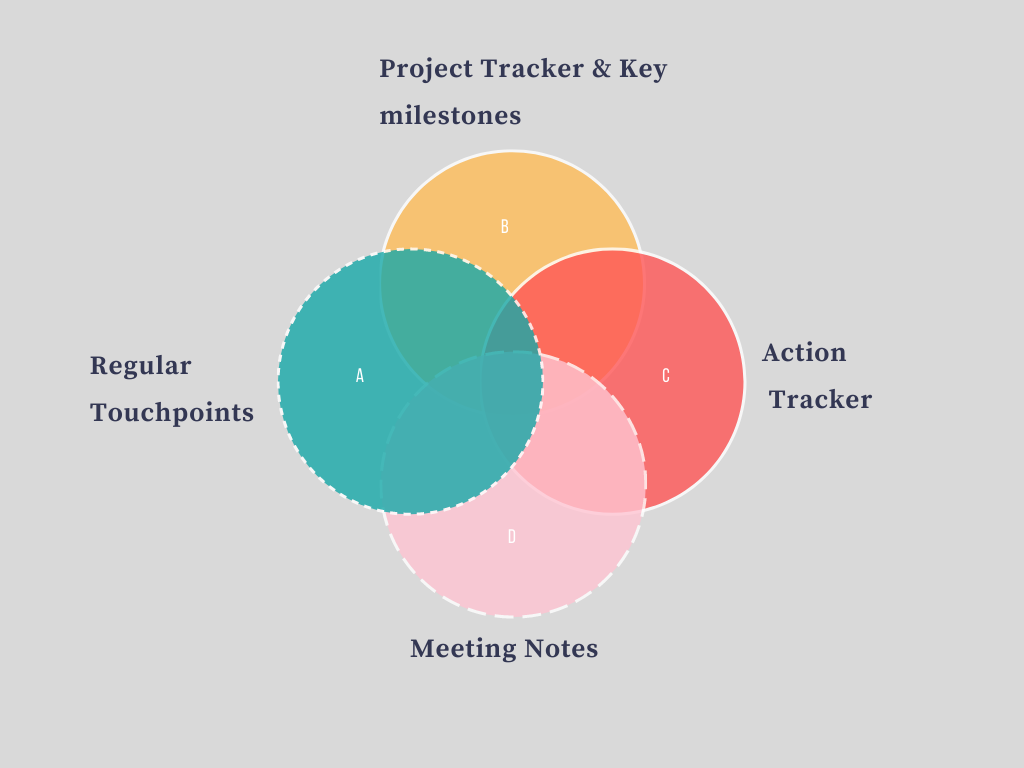
A. Regular Touchpoints: Usually, the mould manufacturing team is different from the one that runs it. Therefore, a touchpoint is critically important to update all the relevant team members with the status of the mould build. Address any specific callouts or requests during these touchpoints.
B. Project Tracker and Key Milestones: The project tracker document highlights overall project timeline and marks the key milestones, some of which are:
- Mould build completion
- Material shipment
- Mould trials
- Mould shipment
There may be additional milestones specific to the particular mould such as the lead time of:
- Assembly machines
- IML machines
- Ancillary equipment
C. Action Tracker: Tracking all the open actions and ensuring that they are resolved before target date helps the team avoid any roll out delays.
D. Meeting Notes: Make an official record of the discussions in the weekly touchpoints. These are useful for future reference. They also serve as a document to support the Project tracker highlighting the key points discussed.
Finally
What begins as an idea in the planning stage starts to take real shape in the commissioning phase. All links in the mould lifecycle management chain have to synchronize with a view to deliver robust, useful, and visually pleasing moulds.
Since its inception, Efficient Innovations has successfully qualified countless Injection & Blow Moulds for a diverse clientele across the globe. We are now an inseparable part of our clients’ Mould Management Team.
All you have to do is get in touch with us at www.efficientinnovations.in to know more !!!