Injection moulding is a plastic manufacturing process that creates high pressure (injection and holding pressure) to mould plastic parts. An injection moulding machine has two units:
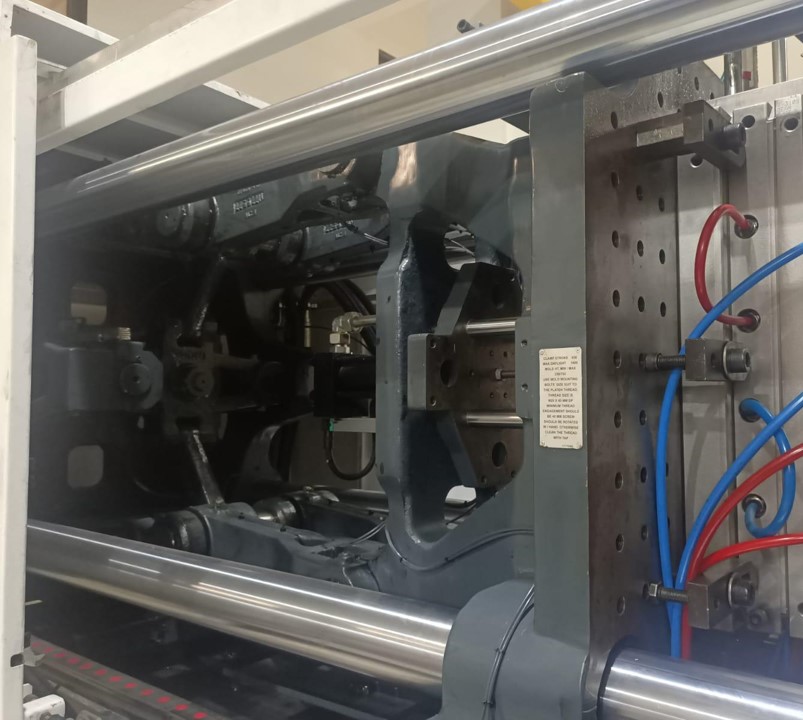
Image 1: Injection Moulding Machine
- Injection Unit: Polymer granules (raw plastic material) are heated and plasticized/homogenised inside the injection barrel. Then, they flow through the nozzle, runner, and gate into the cavity to form the part. As the machine shifts from velocity phase to pressure phase (packing and holding), additional material is pushed into the cavity to minimize sinks and dimensional variation. The clamp must provide sufficient counterforce to balance the immense material pressure inside the cavity.
- Clamping Unit: Brings together the core and the cavity of the mould. Clamping unit applies the clamping force to keep the mould closed i.e. prevent separation of the two mould halves when molten plastic is injected in the mould at high pressure.
Clamping force is usually specified in tons. An 180T (1800kN) injection moulding machine produces a maximum clamping force of 180T. Clamping force calculation determines the selection of the appropriate machine to produce the desired part quality. Successful moulding process depends on the:
- Tonnage applied
- Location of the force
- Type of clamping mechanism
- Size of the mould base
The magnitude of the clamping force is calculated via cavity pressure inside the mould and the projected area over which it acts. The following variables affect the clamping force and are considered for calculation:
- Material Propoerties (MFI)
- Depth of the component (flow length)
- Part Thickness
- Type of runner
Next step is to evaluate the gate size and the number of gates:
- A larger gate diameter has greater area for material to flow through, therefore requiring less pressure from the injection unit to fill and pack the part.
- Number of gates affects the injection pressure during both filling and packing.
If the number and area of gates is large or a part requires a sequential filling, then the required injection pressure will be less and, correspondingly, the mould requires lower clamping tonnage.
Clamping Force Calculation
Following steps are involved in clamping force calculation:
- Projected Area: The first step in calculating the clamping force is to find the surface area (in square inch) of the part and multiply it by the number of the cavities in the mould. If the part has a cored-out surface area (parts with a hole or hollow cylindrical profile), subtract it’s area from the total area.
- Cavity Pressure: Multiply the surface area by cavity pressure (tonnage factor), which is typically between 2 to 10 tons per square inch depending on the material MFI and part geometry. Polypropylene (homo/ copolymer) has 1.5 to 3.5 tonnes/ in2 tonnage factor and that for PET is 2 to 6 tonnes/ in2.
- Runner: If the mould has a cold runner system, add 10% of the total projected area when calculating the clamping force.
- Safety Factor: Add 10% safety factor to the calculated clamping force.
Clamping force = {(surface area of the part X Number of cavities) X (cavity pressure)} X 1.1 (10% safety factor)
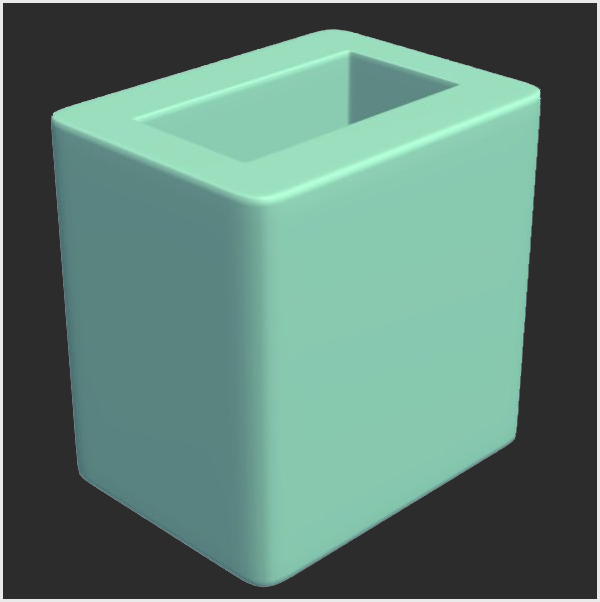
Image 2: Part for Clamping Tonnage Calculation
Example: Consider the part shown in image 2 for clamping tonnage calculation. The part is a rectangle (2 x 4 inch); so the projected area is 8 inch2. Cored out surface area of 1 x 3 = 3 inch2 is subtracted from the projected area. Now, the final projected area is 5inch2. Considering two cavity moulds, cavity pressure of 3 tonnes/ in2 (PP), and depth of 2 inch (have to add 10% safety factor):
Clamping force = [{(5 x 2) x (3)} x 10% for 2inch depth] x 10% safety factor = 36.3T
Other Factors
Following other factors are considered:
- Melt Flow Index: Plastic materials are classified on the basis of their flow characteristics/viscosity. Generally, depending on the part’s application, the material is chosen to provide a desired property to the end product. For e.g. PP is generally chosen for a flip-top cap as it requires excellent hinge property. While calculating clamping force, this is considered as materials with low viscosity have high melt flow and require low clamping force and vice versa.
- Part Depth Dimension: Part depth greater than 1 inch is considered in the calculation. Assume part depth of 2 inches and add 10% force to the calculation.
Potential Causes of Inappropriate Clamp Force
Excessively high or low clamp force can cause part defects and damage the mould or the machine:
Over the long term, excessive clamp force adversely affects the mould, causing rolled parting lines, blocked vents, and cracking of core insert or cavity blocks. Sometimes, it may damage (crack) the mould’s top plate.
- Moulding Defects stem from excessive clamp force and include burn marks, glossy surface, short shots, air bubble, and dimensional differences.
- Moulding Machine’s hydraulic core, mounting plate, and machine plate can deform or even fracture under excessive clamp force.
- Financial Impact worsens as a higher tonnage machine generally costs more to run. A machine with more-than-necessary clamping force can unnecessarily escalate the total job cost. Downtime and repair costs can also add to project expenses.
An experiment to understand the effect of changed clamping force on the part/mould/process parameters revealed that modifying the set clamp force altered the shot weight, cavity pressure, pack rate, and cooling rate. Earlier, a machine operator/engineer considered four plastic variables affecting part dimensions:
- Heat
- Flow
- Pressure
- Cooling
Clamping force was added as the 5th variable after this experiment.
Methods to Optimise Clamping Force
- By Part Weight: Start running a 100% filled and packed out mould to an acceptable (calculated shot weight) level at a higher clamp tonnage. Then, reduce clamp tonnage by 5 to 10% and record the part weight. Mould halves start to separate when the part weight starts rising. By optimizing the clamping force based on part weight, the mould vent easily prevents over clamping and enables energy savings.
- Mould Deflection Sensor: Optimises the clamping force. When the material is being injected into the mould, the sensor shows the quantity of core deflection and gives the user an idea about mould halves separation.
- Measurement: If the part is a rectangle, measure the length, width, and thickness at different clamping tonnage settings. You will observe variation in these dimensions at different settings.
Calculate the clamping force for a given injection mould part at the very beginning of the project! For this is the basis of selecting the correct machine with the required clamping force. Once the mould is ready for production, optimise the clamping tonnage to produce desirable part quality with minimum cost and without impacting the mould and the machine.
Efficient Innovations comes armed with 15+ years of experience in plastic injection moulding. Don’t leave clamping force calculations to the rule of thumb! Connect with us at https://www.efficientinnovations.in/ to optimise your injection moulding process.
Article by
Yagnesh Jethava
Project Engineer
Efficient Innovations Pvt. Ltd.
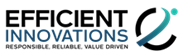