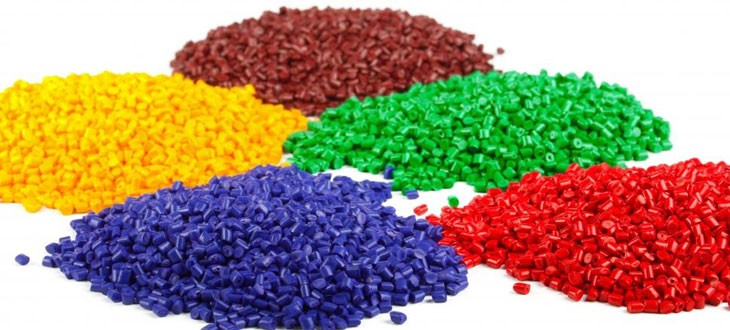
We all are aware of the master-batch (a material that disperses colours) that is added to resin while moulding plastic product for obtaining a coloured product.
The amount or ratio of master-batch added in the resin depends on:
- Intensity of desired colour shade
- Product geometry/volume
- Natural colour/appearance of the resin
- Whether the master-batch is available in liquid or solid form
The ratio of master-batch to resin is called Let Down Ratio, denoted by LDR.
For instance, a 400 ml shampoo bottle cap usually has an LDR of 0.5% – 2%. Whereas a 30 litres bucket has an LDR of around 2% – 4%.
Let us deep dive on LDR with respect to (w.r.t.) to recycled plastic grains or PCR.
Polypropylene (PP) PCR available in the market has a natural, non-uniform grey colour when moulded without master-batch. And, this appearance is not appealing to the consumer, as per the market survey and will not sell readily. A PP – PCR resin usually looks like as shown in the image.
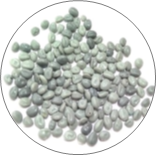
Adding a master-batch with virgin resin to PCR, imparts a pale shade of added colour. For example, when bright colours such as white, yellow, or blue are added with an 0.5-2% LDR, the outcome is light grey, pale yellow and pale bluish grey respectively. This pale appearance is not at all appealing to consumers, especially in the FMCG packaging products. So, for improving appearance, darker colours such as black, shiny grey, dark blue etc. are selected.
Despite using a dark colour, at times, if LDR is kept the same as in virgin resin, the colour obtained is not sufficiently dark or uniform. In such conditions, LDR is usually increased from 0.5-2% to 2-5%, depending upon part geometry and how deep shade is desired.
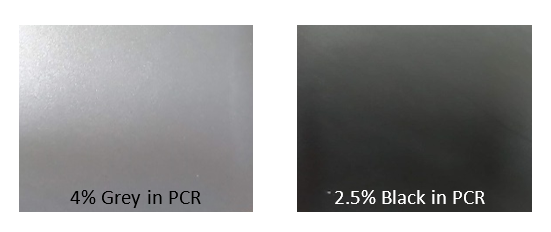
Another question is about the processing conditions. In most cases, there is no change in the processing conditions for this increase in the LDR. Seldom, the tip temperature of the gate area in the hot runner manifold needs to be increased.
Next, upon increasing the LDR to as high as 5% or above, a different complication arises in the part quality. Considering your hot runner has a hot tip (the tip is thermally operated); when the molten mixture of PCR with master-batch is flowing through the tip towards the mould cavities, considerable flow marks surface around the gate area. This is usually noted when moulding a shiny or pearlized master-batch which exhibits a distinctive flow line.
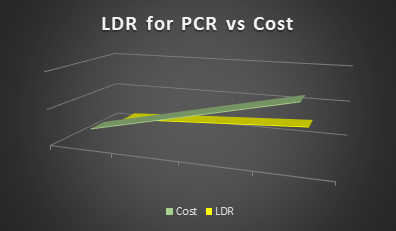
As a result of the high content of master-batch (which is nothing but minerals imparting colours), there is a pigmentation issue which makes the product surface sensitive to external forces. Thus, moulded products show some scuff marks which occur due to rubbing/dashing of parts while ejection.
Then again, there is the issue of gate blemish/ gate blush – a shiny patch that appears around the gate area. This is also a type of flow line.
Most importantly, higher LDR escalates the overall cost per piece.
Such issues are persistent and difficult to eliminate.
But in the end, a recycled resin FMCG package should be accepted despite these minor defects because it is a “Recycled Product”, one step closer towards saving Mother Earth.
We can help!
EIPL is an expert in Sustainable product design and development.
Our Team provides Sustainable solutions right from product design, redesign, or innovation to implementation; and from the prototype phase to its industrial tool qualification. Our skilled and highly experienced team ensures utilization of up-to date technical capabilities and project management techniques in delivering the projects for market launch. We have several years of experience in implementing post consumer resin (PCR) in production at optimized costs by design of the existing packaging products. This has given us an edge as we help clients rapidly attain a sustainability tag. Rigorous follow ups and data accumulation service is also provided for every project.
Moreover, we extensively assist in management and execution of R&D prospects for qualifying Dimensional, Functional and Ergonomic aspects of a product which accelerates the project timeline. We provide a detailed analysis of the process capabilities to ensure the compatibility of PCR grade packaging with Virgin grade packaging.
Our supply chain expertise has been extremely helpful to our clients in the optimal relocation of their assets in relation to their suppliers. A thorough check of the vendor’s compatibility, plant’s design, supply chain documents, quotation, etc. is carried out for successful relocation.
We ensure dedicated resources for smooth communication over the course of the projects. Effective communication skills and people management are our key attributes to connect people across the globe for successful project delivery. EIPL promises excellent value addition, execution of responsibilities, and fully reliable services.
Our team has a global reach in injection moulding. We have acquired vast knowledge and experience over the last 14+ years of working with global leaders of industries in India, and 44+ other countries.
Connect with us on www.efficientinnovations.in to know more!
Article by
Darshak Mehta
Project Manager
EIPL